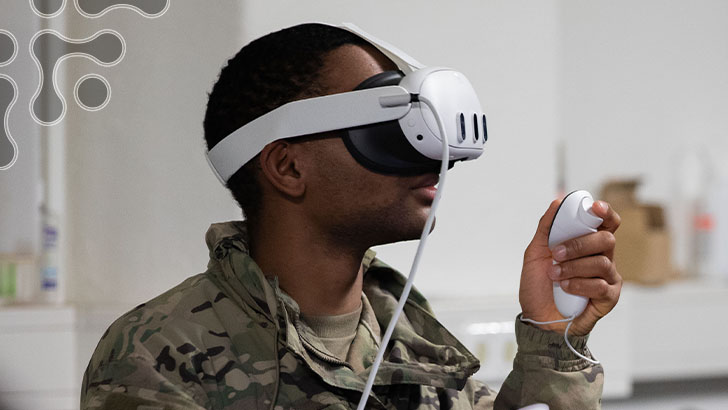
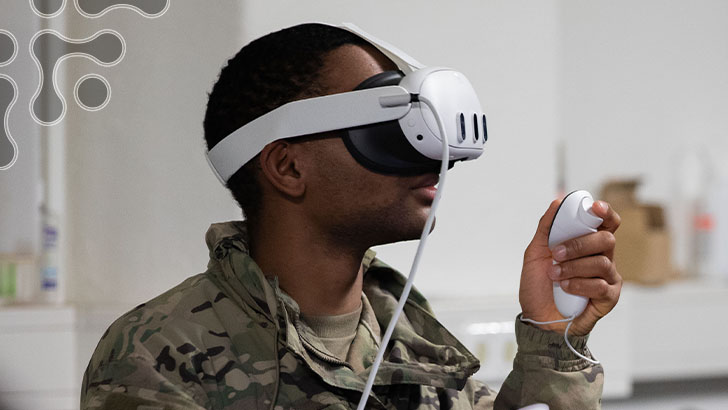
This topic seeks to develop and demonstrate the feasibility of a stand-alone augmented-reality/virtual-reality (AR/VR) system for railroad inspection, maintenance, and training to enhance military logistics and infrastructure repair through real-time visualization and predictive capabilities.
AR and VR technologies can enable real-time, interactive overlays of digital data onto the physical world. They can be fully or partially immersive and offer a wide range of applications that can reduce downtime and increase knowledge for inexperienced users. A recent study by Workplace from Meta in 2022, indicated that up to 45% of frontline workers were planning to leave their job that year alone, impacting the ability to maintain institutional knowledge.
To combat the reduction in knowledge and understanding the need to train new employees in a rapid fashion, companies are modernizing their training methods by adding AR and VR technologies to the training process. A survey conducted by Forbes showed that 86% of respondents had a favorable view of the changes and saw improvement with their quality of the training they received [1].
Traditional methods of railroad track inspection, assessment, and repair are time-consuming, labor-intensive, and require trained and experienced personnel. AR/VR technologies can also be utilized to give military personnel access to important, detailed information, such as schematics, diagnostic data, and repair instructions while working in remote locations.
The Army awarded Microsoft a 10-year contract to modify their Hololens into a mixed reality headset to support the warfighter that can utilize and combine multiple battlefields sensors already used by soldiers. The Hololens is an untethered holographic device that is used by a wide variety of commercial entities such as airlines and auto manufacturers of high-end vehicles to train personnel and improve efficiency of new employees.
The first design was made for civilian use and did not have ruggedized features needed for combat or utilization in the field. According to The Office of the Director, Operational Test and Evaluation (DOT&E), the Integrated Visual Augmentation System (IVAS), the DoD’s version of the Hololens developed by Microsoft, is a head mounted device, worn by soldiers, that includes a see-through heads-up display (HUD), with a variety of sensors used for navigation and operation in low light environments [2].
There have been many issues with advancement and several iterations of the software but “The Army is planning to use IVAS 1.0 systems in its schoolhouses as mission planning tools” [3]. The utilization of the IVAS, will allow maintenance tasks to be completed quicker, reduces errors, and enhances overall operational efficiency, especially in remote or high-risk environments where downtime can be critical [4].
AR and VR technologies are important to include to enhance railroad inspections and maintenance capabilities, particularly for military logistics. The ability to overlay maintenance guidance directly onto equipment and other detailed tasks will enable soldiers to perform their tasks more effectively, without requiring extensive technical expertise [5].
These changes will help create a safer working environment and while enabling soldiers be more adaptable and versatile while handling different types of maintenance on rail and other infrastructure systems. AR and VR technologies will reduce repair times and improve the accuracy of inspections, which strengthens military logistics capabilities and enhances the warfighter’s ability to sustain operations in dynamic, challenging environments.
This topic is only accepting Phase I proposals for a cost up to $250,000 for a 6-month period of performance. Demonstrate the feasibility of using a stand-alone, goggle-based system to detect and identify railroad components, differentiate gauge types, and estimate crater volumes in a remote location or contested environment.
Develop augmented reality, virtual reality, and mixed reality example scenarios to highlight the differences to formulate the best methodology [6]. Deliver a report documenting the research and development efforts along with a detailed description of the proposed methodology.
Program and develop the proposed software technology. Develop a set of small-scale field scenarios to demonstrate the performance of the developed goggle-based system. Apply the proposed visualization methodology to a track in operational condition and a track that has experienced real-world or simulated damage that results in a crater in the crib of the track.
Demonstrate that the technology could be used on a wide range of rail geometries and designs and could estimate crater volumes to generate subgrade and ballast material quantities needed to make repairs. Determine the limitations of performance in the field and field-of-view capabilities of the prototype. Demonstrate the feasibility of using the system in various weather and lighting conditions.
Develop a study that systematically varies the rail gauge, depth of ballast, and volume of missing ballast to determine the conditions for field operations. In addition, determine the environmental stability of the goggle system: relevant variables to consider are temperature effects, corrosion resistance, and battery life.
Deliver a reporting document that includes the development and execution of small-scale scenarios, on various track conditions, displaying the ability of the system to identify track components, the analysis on the ability of the system to accurately estimate fill material quantities, and the environmental stability of the proposed equipment and limitations for use. Provide a field demonstration of Phase II findings.
Yes, there are multiple industries that have already adopted AR/VR or are moving to AR/VR for training and evaluation. There is potential in the railroad industry for track inspection and maintenance and maintenance of locomotives and rail cars. Other infrastructure such as bridges or tunnels could use improvements to field evaluations to increase safety. For military applications, the technology could be used for improving logistics and augmented mission planning and training.
For more information, and to submit your full proposal package, visit the DSIP Portal.
SBIR|STTR Help Desk: usarmy.sbirsttr@army.mil
References:
This topic seeks to develop and demonstrate the feasibility of a stand-alone augmented-reality/virtual-reality (AR/VR) system for railroad inspection, maintenance, and training to enhance military logistics and infrastructure repair through real-time visualization and predictive capabilities.
AR and VR technologies can enable real-time, interactive overlays of digital data onto the physical world. They can be fully or partially immersive and offer a wide range of applications that can reduce downtime and increase knowledge for inexperienced users. A recent study by Workplace from Meta in 2022, indicated that up to 45% of frontline workers were planning to leave their job that year alone, impacting the ability to maintain institutional knowledge.
To combat the reduction in knowledge and understanding the need to train new employees in a rapid fashion, companies are modernizing their training methods by adding AR and VR technologies to the training process. A survey conducted by Forbes showed that 86% of respondents had a favorable view of the changes and saw improvement with their quality of the training they received [1].
Traditional methods of railroad track inspection, assessment, and repair are time-consuming, labor-intensive, and require trained and experienced personnel. AR/VR technologies can also be utilized to give military personnel access to important, detailed information, such as schematics, diagnostic data, and repair instructions while working in remote locations.
The Army awarded Microsoft a 10-year contract to modify their Hololens into a mixed reality headset to support the warfighter that can utilize and combine multiple battlefields sensors already used by soldiers. The Hololens is an untethered holographic device that is used by a wide variety of commercial entities such as airlines and auto manufacturers of high-end vehicles to train personnel and improve efficiency of new employees.
The first design was made for civilian use and did not have ruggedized features needed for combat or utilization in the field. According to The Office of the Director, Operational Test and Evaluation (DOT&E), the Integrated Visual Augmentation System (IVAS), the DoD’s version of the Hololens developed by Microsoft, is a head mounted device, worn by soldiers, that includes a see-through heads-up display (HUD), with a variety of sensors used for navigation and operation in low light environments [2].
There have been many issues with advancement and several iterations of the software but “The Army is planning to use IVAS 1.0 systems in its schoolhouses as mission planning tools” [3]. The utilization of the IVAS, will allow maintenance tasks to be completed quicker, reduces errors, and enhances overall operational efficiency, especially in remote or high-risk environments where downtime can be critical [4].
AR and VR technologies are important to include to enhance railroad inspections and maintenance capabilities, particularly for military logistics. The ability to overlay maintenance guidance directly onto equipment and other detailed tasks will enable soldiers to perform their tasks more effectively, without requiring extensive technical expertise [5].
These changes will help create a safer working environment and while enabling soldiers be more adaptable and versatile while handling different types of maintenance on rail and other infrastructure systems. AR and VR technologies will reduce repair times and improve the accuracy of inspections, which strengthens military logistics capabilities and enhances the warfighter’s ability to sustain operations in dynamic, challenging environments.
This topic is only accepting Phase I proposals for a cost up to $250,000 for a 6-month period of performance. Demonstrate the feasibility of using a stand-alone, goggle-based system to detect and identify railroad components, differentiate gauge types, and estimate crater volumes in a remote location or contested environment.
Develop augmented reality, virtual reality, and mixed reality example scenarios to highlight the differences to formulate the best methodology [6]. Deliver a report documenting the research and development efforts along with a detailed description of the proposed methodology.
Program and develop the proposed software technology. Develop a set of small-scale field scenarios to demonstrate the performance of the developed goggle-based system. Apply the proposed visualization methodology to a track in operational condition and a track that has experienced real-world or simulated damage that results in a crater in the crib of the track.
Demonstrate that the technology could be used on a wide range of rail geometries and designs and could estimate crater volumes to generate subgrade and ballast material quantities needed to make repairs. Determine the limitations of performance in the field and field-of-view capabilities of the prototype. Demonstrate the feasibility of using the system in various weather and lighting conditions.
Develop a study that systematically varies the rail gauge, depth of ballast, and volume of missing ballast to determine the conditions for field operations. In addition, determine the environmental stability of the goggle system: relevant variables to consider are temperature effects, corrosion resistance, and battery life.
Deliver a reporting document that includes the development and execution of small-scale scenarios, on various track conditions, displaying the ability of the system to identify track components, the analysis on the ability of the system to accurately estimate fill material quantities, and the environmental stability of the proposed equipment and limitations for use. Provide a field demonstration of Phase II findings.
Yes, there are multiple industries that have already adopted AR/VR or are moving to AR/VR for training and evaluation. There is potential in the railroad industry for track inspection and maintenance and maintenance of locomotives and rail cars. Other infrastructure such as bridges or tunnels could use improvements to field evaluations to increase safety. For military applications, the technology could be used for improving logistics and augmented mission planning and training.
For more information, and to submit your full proposal package, visit the DSIP Portal.
SBIR|STTR Help Desk: usarmy.sbirsttr@army.mil
References: