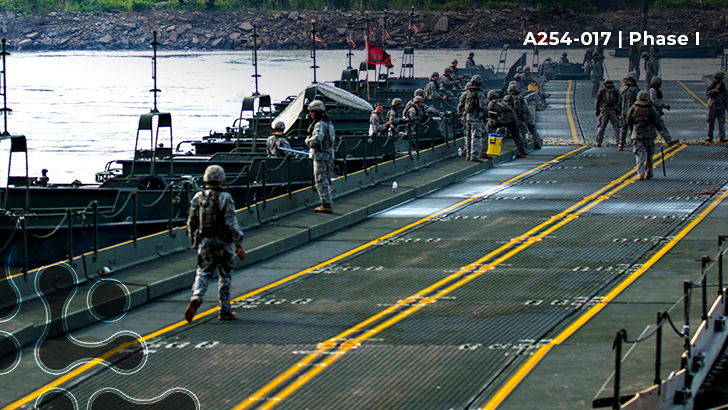
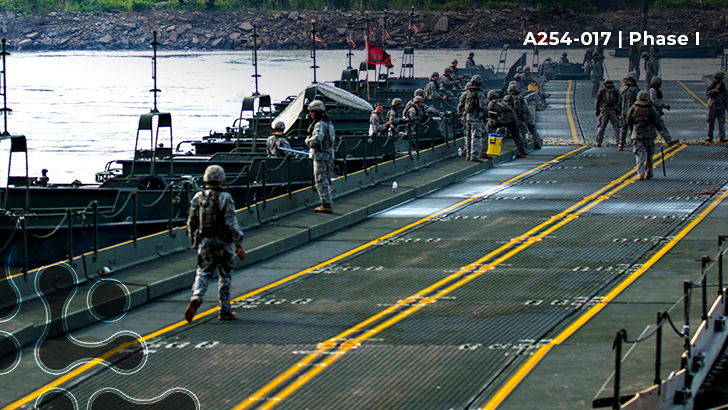
We are no longer accepting white papers. SBIR submissions are now limited to those eligible through the xTech competition.
IMPORTANT: xTechIgnite will be used to identify small business concerns that meet the criteria for award. Winners selected from the xTechIgnite prize competition will be the only firms eligible to submit an SBIR proposal under any of the topics listed above. Proposals submitted to the topics listed above by nonwinners of the xTechIgnite competition will not be evaluated. See the full xTechIgnite competition RFI here: https://www.xtech.army.mil/competition/xtechignite/.
The white paper submission deadline for xTechIgnite is March 12, 2025. White papers must be submitted by following instructions provided at the xTechIgnite link above. NOTE: white papers are NOT submitted to DSIP. Small business concerns that do not submit a concept white paper to the xTechIgnite competition before the March 12, 2025 deadline will be ineligible to compete or submit a full SBIR proposal to DSIP.
Objective
The current methods for assessing military bridges rely on Preventative Maintenance Check and Services (PMCS) combined with fatigue monitoring crack gauges, which have proven insufficient for accurately determining a bridge’s remaining service life. This inaccuracy forces the Army to maintain a surplus of bridges to mitigate the risk of unexpected failures. Research highlights that vehicle crossings, rather than environmental factors, are the primary determinants of bridge health, with the impact varying significantly by vehicle type.
To address this, the Bridge Health Monitoring (BHM) system seeks to revolutionize bridge assessment and management through an integrated approach combining advanced sensor technology, onboard data storage, and adaptable communication capabilities. By continuously monitoring and recording vehicle traffic, structural stress, and environmental conditions, the BHM system will enable precise predictions of a bridge’s remaining service life. This innovation promises to reduce reliance on manual inspections, enhance situational awareness for battlefield commanders, and optimize bridge asset utilization, ensuring military readiness and operational efficiency.
Description
The Bridge Health Monitoring (BHM) project will develop a robust, modular, and scalable technology suite for real-time monitoring and assessment of military and commercial bridge health. This integrated system will empower battlefield commanders and sustainers by providing actionable insights into bridge readiness and lifespan. The proposed solution should address a combination of advanced sensors, onboard storage systems, and secure communication technologies to achieve the following objectives:
1. Types of Bridges
2. Real-time and Periodic Monitoring
The BHM system will monitor key indicators of structural integrity, including stress, fatigue, and damage, through a modular sensor suite. While real-time communication may be beneficial for specific use cases (e.g., commercial highway bridges), the primary focus is on:
3. Predictive Analytics and Storage Monitoring
In addition to operational bridges, the BHM system must maintain information on the health of portable bridges during storage. This capability ensures readiness for deployment. Predictive analytics should incorporate:
4. Indefinite Data Storage and Management
The system must include a robust mechanism for the indefinite storage of bridge health data. This includes maintaining detailed historical records of usage, environmental exposure, and maintenance activities. The solution should employ secure, scalable storage systems, ensuring data integrity and accessibility for lifecycle management and continuous improvement.
5. Sensor Suite Requirements
The sensor package must be:
6. Energy Efficiency and Environmental Resilience
The solution must function autonomously with portable power sources for mobile bridges and integrate with fixed power systems for stationary bridges. Sensors must operate reliably in diverse and challenging environments, from combat zones to urban areas.
7. Secure, Adaptable Data Communication
Data collected by the system will be securely transmitted when necessary. For initial feasibility, the focus is on:
IMPORTANT: A prize competition, xTechIgnite, will be used to identify small business concerns that meet the criteria for award for this topic. Winners selected from the xTechIgnite prize competition will be the only firms eligible to submit a SBIR proposal under this topic. All other proposals will not be evaluated. See the full xTechIgnite competition details here: https://www.xtech.army.mil/competition/xtechignite/.
Phase I
This topic is only accepting Phase I proposals for a cost up to $250,000 for a 6-month period of performance.
Phase I of the Bridge Health Monitoring (BHM) project will culminate in a comprehensive report that explores the various aspects of the system. The report will provide an in-depth analysis of the sensor technologies evaluated for potential use in the solution, including the selected sensors and the rationale behind their choice.
The study will also delve into the critical aspects of bridge health communication, power supply, and data management. Specifically, it will address how bridge health information will be transmitted to Commanders and Maintainers in an electronically monitored environment, ensuring seamless integration and situational awareness without undue risk. Additionally, the report will outline the power supply requirements for the BHM system and propose a solution for maintaining bridge health data continuity, regardless of whether the bridge is deployed or stored in a facility.
While the primary focus of the SBIR is on developing a BHM solution for the Heavy Assault Scissor Bridge (HASB), the Phase I investigation will also examine the potential for commonality across Army Bridge systems. The study will identify the essential components that must remain with a bridge and those that could be removed and adapted for use on other bridge types, thereby promoting a level of standardization and interoperability across the Army’s bridge inventory.
The Phase I report will provide a thorough understanding of the BHM system’s requirements, capabilities, and potential for scalability, laying the foundation for the development of a robust and effective bridge health monitoring solution.
Phase II
Phase II of the Bridge Health Monitoring (BHM) project will focus on the fabrication and testing of a prototype system, building on the research and analysis conducted in Phase I. A key aspect of this phase will be the implementation of robust cyber security measures to ensure the system’s integrity and protect against potential threats.
In addition to prototype development, the vendor will conduct a comprehensive sustainability assessment of the selected components to guarantee a viable path for long-term support and maintenance. This assessment will ensure that the chosen technical solutions can be supported and upgraded over time, minimizing the risk of obsolescence and ensuring the system’s continued effectiveness.
The prototype development process will involve the creation of off-bridge components and breadboard systems, which will be thoroughly tested and optimized to ensure seamless integration and performance. The final prototype will be designed to be compatible with the Heavy Assault Scissor Bridge (HASB) and will include all necessary equipment to function as proposed.
In collaboration with the PdM Bridging team and the GVSC Bridge Technology Lab, the prototype will undergo rigorous validation and testing on a HASB to ensure its performance and accuracy. The vendor will also conduct a live demonstration of the solution at Fort Leonard Wood, showcasing its capabilities on a local bridge.
The deliverables for Phase II will include two complete systems, which will support additional field evaluations and testing. These systems will provide the Army with a tangible, functional solution for monitoring bridge health, enabling more informed decision-making and improved maintenance practices.
Phase III
Submission Information
For more information, and to submit your full proposal package, visit the DSIP Portal.
SBIR|STTR Help Desk: usarmy.sbirsttr@army.mil
References:
We are no longer accepting white papers. SBIR submissions are now limited to those eligible through the xTech competition.
IMPORTANT: xTechIgnite will be used to identify small business concerns that meet the criteria for award. Winners selected from the xTechIgnite prize competition will be the only firms eligible to submit an SBIR proposal under any of the topics listed above. Proposals submitted to the topics listed above by nonwinners of the xTechIgnite competition will not be evaluated. See the full xTechIgnite competition RFI here: https://www.xtech.army.mil/competition/xtechignite/.
The white paper submission deadline for xTechIgnite is March 12, 2025. White papers must be submitted by following instructions provided at the xTechIgnite link above. NOTE: white papers are NOT submitted to DSIP. Small business concerns that do not submit a concept white paper to the xTechIgnite competition before the March 12, 2025 deadline will be ineligible to compete or submit a full SBIR proposal to DSIP.
Objective
The current methods for assessing military bridges rely on Preventative Maintenance Check and Services (PMCS) combined with fatigue monitoring crack gauges, which have proven insufficient for accurately determining a bridge’s remaining service life. This inaccuracy forces the Army to maintain a surplus of bridges to mitigate the risk of unexpected failures. Research highlights that vehicle crossings, rather than environmental factors, are the primary determinants of bridge health, with the impact varying significantly by vehicle type.
To address this, the Bridge Health Monitoring (BHM) system seeks to revolutionize bridge assessment and management through an integrated approach combining advanced sensor technology, onboard data storage, and adaptable communication capabilities. By continuously monitoring and recording vehicle traffic, structural stress, and environmental conditions, the BHM system will enable precise predictions of a bridge’s remaining service life. This innovation promises to reduce reliance on manual inspections, enhance situational awareness for battlefield commanders, and optimize bridge asset utilization, ensuring military readiness and operational efficiency.
Description
The Bridge Health Monitoring (BHM) project will develop a robust, modular, and scalable technology suite for real-time monitoring and assessment of military and commercial bridge health. This integrated system will empower battlefield commanders and sustainers by providing actionable insights into bridge readiness and lifespan. The proposed solution should address a combination of advanced sensors, onboard storage systems, and secure communication technologies to achieve the following objectives:
1. Types of Bridges
2. Real-time and Periodic Monitoring
The BHM system will monitor key indicators of structural integrity, including stress, fatigue, and damage, through a modular sensor suite. While real-time communication may be beneficial for specific use cases (e.g., commercial highway bridges), the primary focus is on:
3. Predictive Analytics and Storage Monitoring
In addition to operational bridges, the BHM system must maintain information on the health of portable bridges during storage. This capability ensures readiness for deployment. Predictive analytics should incorporate:
4. Indefinite Data Storage and Management
The system must include a robust mechanism for the indefinite storage of bridge health data. This includes maintaining detailed historical records of usage, environmental exposure, and maintenance activities. The solution should employ secure, scalable storage systems, ensuring data integrity and accessibility for lifecycle management and continuous improvement.
5. Sensor Suite Requirements
The sensor package must be:
6. Energy Efficiency and Environmental Resilience
The solution must function autonomously with portable power sources for mobile bridges and integrate with fixed power systems for stationary bridges. Sensors must operate reliably in diverse and challenging environments, from combat zones to urban areas.
7. Secure, Adaptable Data Communication
Data collected by the system will be securely transmitted when necessary. For initial feasibility, the focus is on:
IMPORTANT: A prize competition, xTechIgnite, will be used to identify small business concerns that meet the criteria for award for this topic. Winners selected from the xTechIgnite prize competition will be the only firms eligible to submit a SBIR proposal under this topic. All other proposals will not be evaluated. See the full xTechIgnite competition details here: https://www.xtech.army.mil/competition/xtechignite/.
Phase I
This topic is only accepting Phase I proposals for a cost up to $250,000 for a 6-month period of performance.
Phase I of the Bridge Health Monitoring (BHM) project will culminate in a comprehensive report that explores the various aspects of the system. The report will provide an in-depth analysis of the sensor technologies evaluated for potential use in the solution, including the selected sensors and the rationale behind their choice.
The study will also delve into the critical aspects of bridge health communication, power supply, and data management. Specifically, it will address how bridge health information will be transmitted to Commanders and Maintainers in an electronically monitored environment, ensuring seamless integration and situational awareness without undue risk. Additionally, the report will outline the power supply requirements for the BHM system and propose a solution for maintaining bridge health data continuity, regardless of whether the bridge is deployed or stored in a facility.
While the primary focus of the SBIR is on developing a BHM solution for the Heavy Assault Scissor Bridge (HASB), the Phase I investigation will also examine the potential for commonality across Army Bridge systems. The study will identify the essential components that must remain with a bridge and those that could be removed and adapted for use on other bridge types, thereby promoting a level of standardization and interoperability across the Army’s bridge inventory.
The Phase I report will provide a thorough understanding of the BHM system’s requirements, capabilities, and potential for scalability, laying the foundation for the development of a robust and effective bridge health monitoring solution.
Phase II
Phase II of the Bridge Health Monitoring (BHM) project will focus on the fabrication and testing of a prototype system, building on the research and analysis conducted in Phase I. A key aspect of this phase will be the implementation of robust cyber security measures to ensure the system’s integrity and protect against potential threats.
In addition to prototype development, the vendor will conduct a comprehensive sustainability assessment of the selected components to guarantee a viable path for long-term support and maintenance. This assessment will ensure that the chosen technical solutions can be supported and upgraded over time, minimizing the risk of obsolescence and ensuring the system’s continued effectiveness.
The prototype development process will involve the creation of off-bridge components and breadboard systems, which will be thoroughly tested and optimized to ensure seamless integration and performance. The final prototype will be designed to be compatible with the Heavy Assault Scissor Bridge (HASB) and will include all necessary equipment to function as proposed.
In collaboration with the PdM Bridging team and the GVSC Bridge Technology Lab, the prototype will undergo rigorous validation and testing on a HASB to ensure its performance and accuracy. The vendor will also conduct a live demonstration of the solution at Fort Leonard Wood, showcasing its capabilities on a local bridge.
The deliverables for Phase II will include two complete systems, which will support additional field evaluations and testing. These systems will provide the Army with a tangible, functional solution for monitoring bridge health, enabling more informed decision-making and improved maintenance practices.
Phase III
Submission Information
For more information, and to submit your full proposal package, visit the DSIP Portal.
SBIR|STTR Help Desk: usarmy.sbirsttr@army.mil
References: