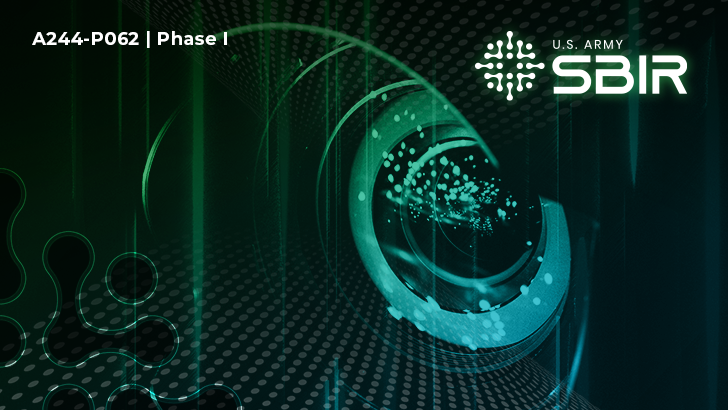
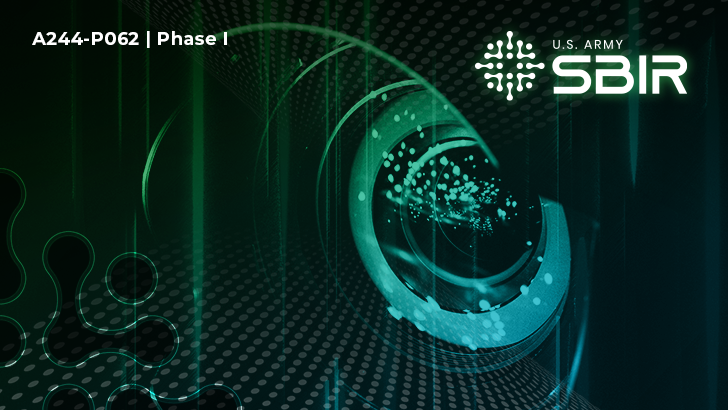
Objective
The Army SBIR Program is searching for innovative solutions related to improving performance and size, weight, power, and cost (SWAP-C) and/or address supply chain issues for components of uncooled longwave infrared thermal sensors.
Description
This topic accepts Phase I proposals submissions for a cost up to $250,000 for a 6-month period of performance.
This open topic accepts only phase I submissions. The scope of this open topic is limited to resistive bolometric-type sensors and their supporting components. Bolometers are a microelectromechanical structure (MEMS) enabling detection of thermal radiation without the need to cool the sensor to cryogenic temperatures. Alternate sensing technologies (i.e., not resistive bolometers) are excluded.
The Army SBIR Program seeks proposals that focus on one or more of the following sub-topics within uncooled infrared sensors to improve the sensor or fortify a strong industrial base for sensor components. Firms are asked to self-identify which sub-topic(s) their technology relates to in their proposal submission.
Phase I
Develop an initial design of your proposed component technology with stakeholder input focusing on burning down the highest risk items and building confidence in a future complete design. Support with appropriate modeling, simulation, engineering, or other justification to demonstrate feasibility.
Analyze the potential impact of your component technology to the uncooled sensor “ecosystem” in terms of sensor size, weight, power, cost, performance, and assured supply chain. With stakeholder input and these potential impacts in mind, define your metrics of success and specific deliverable for a phase 2 effort.
Discuss how your technology could potentially impact the warfighters’ ability to perform or enable their mission. Describe what supporting infrastructure and inputs your component technology will require to transition into full rate production, e.g., manufacturing tools, materials, training data, computational resources, or others as required. Generate an initial transition plan for your component technology including possible partners.
Phase II
Leveraging phase 1 results, design, fabricate, and deliver the prototype hardware and/or software defined in phase 1. Refine success metrics, if necessary. Define a test plan and characterize the prototype against relevant technical and defined success metrics and deliver the results in a technical data package. Define and document relevant interfaces.
Mature the transition and production plan and attempt to partner with relevant organizations such as Primes or manufacturing and integration partners. Deliver a prototype that is mature enough to enable a technology transition to the Army or relevant integrators. If relevant, the prototype should be ready to spin into low-rate initial production at the sub-component level.
Phase III
Submission Information
For more information, and to submit your full proposal package, visit the DSIP Portal.
SBIR|STTR Help Desk: usarmy.sbirsttr@army.mil
References:
Objective
The Army SBIR Program is searching for innovative solutions related to improving performance and size, weight, power, and cost (SWAP-C) and/or address supply chain issues for components of uncooled longwave infrared thermal sensors.
Description
This topic accepts Phase I proposals submissions for a cost up to $250,000 for a 6-month period of performance.
This open topic accepts only phase I submissions. The scope of this open topic is limited to resistive bolometric-type sensors and their supporting components. Bolometers are a microelectromechanical structure (MEMS) enabling detection of thermal radiation without the need to cool the sensor to cryogenic temperatures. Alternate sensing technologies (i.e., not resistive bolometers) are excluded.
The Army SBIR Program seeks proposals that focus on one or more of the following sub-topics within uncooled infrared sensors to improve the sensor or fortify a strong industrial base for sensor components. Firms are asked to self-identify which sub-topic(s) their technology relates to in their proposal submission.
Phase I
Develop an initial design of your proposed component technology with stakeholder input focusing on burning down the highest risk items and building confidence in a future complete design. Support with appropriate modeling, simulation, engineering, or other justification to demonstrate feasibility.
Analyze the potential impact of your component technology to the uncooled sensor “ecosystem” in terms of sensor size, weight, power, cost, performance, and assured supply chain. With stakeholder input and these potential impacts in mind, define your metrics of success and specific deliverable for a phase 2 effort.
Discuss how your technology could potentially impact the warfighters’ ability to perform or enable their mission. Describe what supporting infrastructure and inputs your component technology will require to transition into full rate production, e.g., manufacturing tools, materials, training data, computational resources, or others as required. Generate an initial transition plan for your component technology including possible partners.
Phase II
Leveraging phase 1 results, design, fabricate, and deliver the prototype hardware and/or software defined in phase 1. Refine success metrics, if necessary. Define a test plan and characterize the prototype against relevant technical and defined success metrics and deliver the results in a technical data package. Define and document relevant interfaces.
Mature the transition and production plan and attempt to partner with relevant organizations such as Primes or manufacturing and integration partners. Deliver a prototype that is mature enough to enable a technology transition to the Army or relevant integrators. If relevant, the prototype should be ready to spin into low-rate initial production at the sub-component level.
Phase III
Submission Information
For more information, and to submit your full proposal package, visit the DSIP Portal.
SBIR|STTR Help Desk: usarmy.sbirsttr@army.mil
References: