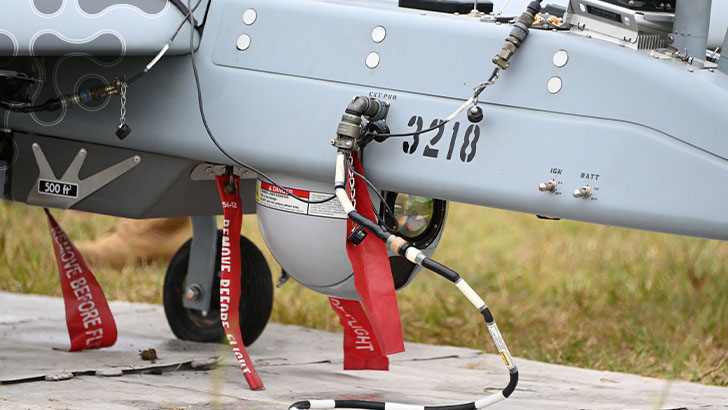
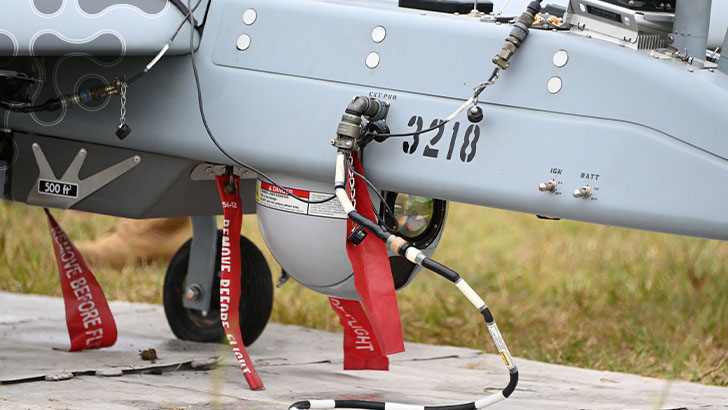
Army is seeking emerging optical material platforms that provide energy efficient modulation at cryogenic temperatures. This effort will develop emerging photonic components for cryogenic application alongside high-performance infrared sensor arrays.
Our Warfighters rely on an ever-increasing amount of data to perform the mission. Individual sensors, such as high-definition thermal cameras, counter-UAV sensors, and advanced radio frequency spectrum analyzers, all generate many gigabytes of data per second. Moving data between sensor and processor, around the vehicle, or between command posts is most effectively done via optical fiber. Optical data transport benefits from decades of commercial development, leading to lower power, faster communications, and higher bandwidth when compared to electrical signals. However, just as getting fiber to individual households was the “last mile” challenge for internet availability, getting fiber to where the data is generated is the photonics challenge for today’s military.
Laboratory demonstrations have shown that electrical outputs from high resolution sensors can successfully be converted to optical data transmission utilizing optical modulators. This enables a drastic increase in data transmission rates, superior energy efficiency, and flexible fiber routing to downstream Artificial Intelligence computer electronics. Optical conversion permits system designers to push beyond current resolution, frame rate, functionality and bit depth limitations, providing the DoD a leap-ahead capability with advances in ultra-large format sensors, wide field-of-view systems, and fast-event detection providing value to a multitude of detect, decide, track and reconnaissance missions.
The electro-optic modulator (EOM) is a core component within an optical signal processing chain. An EOM can be made of a variety of materials and can be based on a number of physical effects, such as the Pockels effect, plasma dispersion effect, DC Kerr effect, and the Franz-Keldysh effect. Many EOM materials and related components (laser, transceiver, etc.) have benefited greatly from datacom and telecom industries.
Enormous data rates and excellent energy efficiency are achievable with several EOM solutions, but offerings are primarily intended for room temperature use and are susceptible to performance degradation at cryogenic temperatures. The most mature foundry offering to date has been the silicon photonics (SiPh) micro-ring resonator. SiPh modulators are susceptible to carrier-freeze out at low temperature and operate at a very narrow wavelength bandwidth. For system adoption, an EOM solution that exhibits superior robustness of operation and resilience or performance improvement at cryogenic temperatures is desirable.
We are seeking EOM material platform solutions that exhibit excellent modulation efficiency at low temperatures (< 100 K) required for adoption into high performance Army infrared imaging systems. Excellent energy efficiency, compact physical size, low bit error rate (<1E-10), and low voltage biasing are key considerations for development of the most appropriate EOM solution. EOM solutions must be able to achieve high aggregate data rates (> 20 Gbps) and have viable scalability to higher data rates.
Compatible integration alongside mixed signal digital read-out integrated circuit (DROIC) components is a key consideration in identifying the best solution. Modulator drive voltages should be appropriately aligned with existing DROIC I/O voltages. While this work focuses on the development of cryogenic optical modulator materials, topics must also consider a pathway for integration into existing foundry processes. Technologies that have the potential to mature to standard foundry offerings will be received favorably.
This topic is only accepting Phase I proposals for a cost up to $250,000 for a 6-month period of performance. In Phase I, performers will describe, develop, and begin fabrication of EOM solutions for use in cryogenic environment. This phase can include material device design, modeling, platform and process fabrication improvements, and system level architecture considerations.
Additionally, performers will begin preliminary work in identifying hardware and software required for conversion of digital data to optical output link in an appropriate cryostat environment for demonstration effort in Phase II. In all cases, energy per bit and total system energy costs should be minimized. By the end of Phase I, performers are expected to have comprehensive plan for EOM fabrication, improvement, and demonstration in Phase II.
In Phase II, performers will fabricate and refine necessary photonic components to begin bit error rate testing at cryogenic temperatures. This will likely include multiple fabrication runs, improvements in design and/or processing, and advanced manufacturability of the material platform. Test temperatures range for consideration is between 20K – 150K.
Understanding of drive voltages, system coupling, insertion, and chip-to-chip losses should be documented in this phase to better understand system energy budget when implementing this technology alongside advanced infrared Army imaging systems. The Phase II deliverable includes a developed test chip and full cryogenic performance report to include bit error rate test and system power budget analysis.
Depending on initial maturity, the project must also make progress towards making the fabricated EOM compatible with current and future foundry processes and material platforms. This could be represented by a proof-of-concept demonstration or a detailed analysis of existing processing opportunities that would make this EOM technology a standard offering at a domestic foundry.
Phase II will also include engagement with camera system vendors that provide relevant DROIC components to Army programs. This engagement will bring down the risk of interfacing the proposed EOM solution within an Army infrared imaging product by ensuring this technology can be driven either directly from the DROIC I/O, or less preferably via an intermediary bias board that can supply the required voltages to operate the EOM.
Cryogenic optical modulators could have use for commercial quantum computer technologies.
For more information, and to submit your full proposal package, visit the DSIP Portal.
SBIR|STTR Help Desk: usarmy.sbirsttr@army.mil
References:
Army is seeking emerging optical material platforms that provide energy efficient modulation at cryogenic temperatures. This effort will develop emerging photonic components for cryogenic application alongside high-performance infrared sensor arrays.
Our Warfighters rely on an ever-increasing amount of data to perform the mission. Individual sensors, such as high-definition thermal cameras, counter-UAV sensors, and advanced radio frequency spectrum analyzers, all generate many gigabytes of data per second. Moving data between sensor and processor, around the vehicle, or between command posts is most effectively done via optical fiber. Optical data transport benefits from decades of commercial development, leading to lower power, faster communications, and higher bandwidth when compared to electrical signals. However, just as getting fiber to individual households was the “last mile” challenge for internet availability, getting fiber to where the data is generated is the photonics challenge for today’s military.
Laboratory demonstrations have shown that electrical outputs from high resolution sensors can successfully be converted to optical data transmission utilizing optical modulators. This enables a drastic increase in data transmission rates, superior energy efficiency, and flexible fiber routing to downstream Artificial Intelligence computer electronics. Optical conversion permits system designers to push beyond current resolution, frame rate, functionality and bit depth limitations, providing the DoD a leap-ahead capability with advances in ultra-large format sensors, wide field-of-view systems, and fast-event detection providing value to a multitude of detect, decide, track and reconnaissance missions.
The electro-optic modulator (EOM) is a core component within an optical signal processing chain. An EOM can be made of a variety of materials and can be based on a number of physical effects, such as the Pockels effect, plasma dispersion effect, DC Kerr effect, and the Franz-Keldysh effect. Many EOM materials and related components (laser, transceiver, etc.) have benefited greatly from datacom and telecom industries.
Enormous data rates and excellent energy efficiency are achievable with several EOM solutions, but offerings are primarily intended for room temperature use and are susceptible to performance degradation at cryogenic temperatures. The most mature foundry offering to date has been the silicon photonics (SiPh) micro-ring resonator. SiPh modulators are susceptible to carrier-freeze out at low temperature and operate at a very narrow wavelength bandwidth. For system adoption, an EOM solution that exhibits superior robustness of operation and resilience or performance improvement at cryogenic temperatures is desirable.
We are seeking EOM material platform solutions that exhibit excellent modulation efficiency at low temperatures (< 100 K) required for adoption into high performance Army infrared imaging systems. Excellent energy efficiency, compact physical size, low bit error rate (<1E-10), and low voltage biasing are key considerations for development of the most appropriate EOM solution. EOM solutions must be able to achieve high aggregate data rates (> 20 Gbps) and have viable scalability to higher data rates.
Compatible integration alongside mixed signal digital read-out integrated circuit (DROIC) components is a key consideration in identifying the best solution. Modulator drive voltages should be appropriately aligned with existing DROIC I/O voltages. While this work focuses on the development of cryogenic optical modulator materials, topics must also consider a pathway for integration into existing foundry processes. Technologies that have the potential to mature to standard foundry offerings will be received favorably.
This topic is only accepting Phase I proposals for a cost up to $250,000 for a 6-month period of performance. In Phase I, performers will describe, develop, and begin fabrication of EOM solutions for use in cryogenic environment. This phase can include material device design, modeling, platform and process fabrication improvements, and system level architecture considerations.
Additionally, performers will begin preliminary work in identifying hardware and software required for conversion of digital data to optical output link in an appropriate cryostat environment for demonstration effort in Phase II. In all cases, energy per bit and total system energy costs should be minimized. By the end of Phase I, performers are expected to have comprehensive plan for EOM fabrication, improvement, and demonstration in Phase II.
In Phase II, performers will fabricate and refine necessary photonic components to begin bit error rate testing at cryogenic temperatures. This will likely include multiple fabrication runs, improvements in design and/or processing, and advanced manufacturability of the material platform. Test temperatures range for consideration is between 20K – 150K.
Understanding of drive voltages, system coupling, insertion, and chip-to-chip losses should be documented in this phase to better understand system energy budget when implementing this technology alongside advanced infrared Army imaging systems. The Phase II deliverable includes a developed test chip and full cryogenic performance report to include bit error rate test and system power budget analysis.
Depending on initial maturity, the project must also make progress towards making the fabricated EOM compatible with current and future foundry processes and material platforms. This could be represented by a proof-of-concept demonstration or a detailed analysis of existing processing opportunities that would make this EOM technology a standard offering at a domestic foundry.
Phase II will also include engagement with camera system vendors that provide relevant DROIC components to Army programs. This engagement will bring down the risk of interfacing the proposed EOM solution within an Army infrared imaging product by ensuring this technology can be driven either directly from the DROIC I/O, or less preferably via an intermediary bias board that can supply the required voltages to operate the EOM.
Cryogenic optical modulators could have use for commercial quantum computer technologies.
For more information, and to submit your full proposal package, visit the DSIP Portal.
SBIR|STTR Help Desk: usarmy.sbirsttr@army.mil
References: