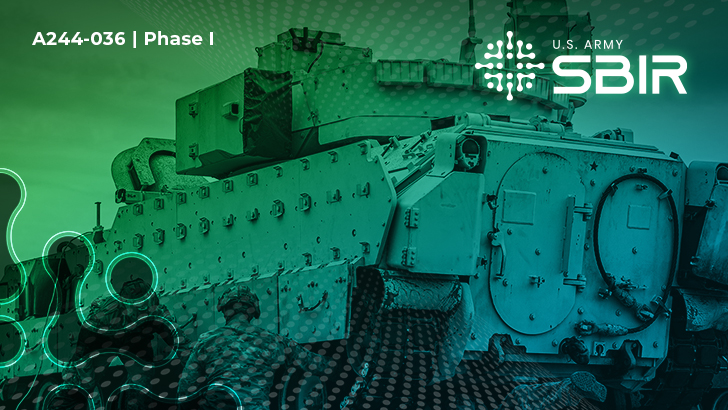
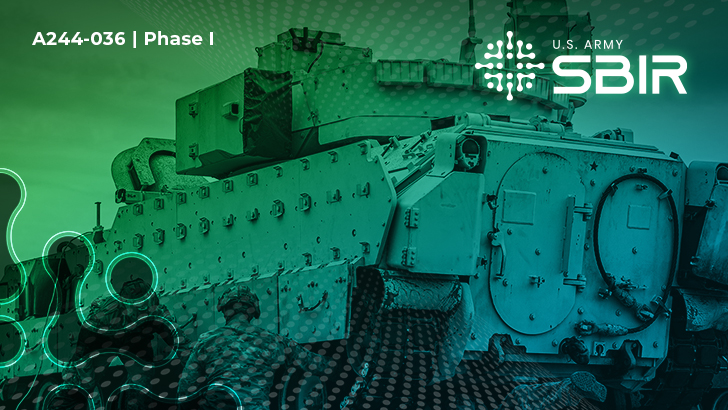
Selectees
Objective
The Army is seeking low-cost, high-yield domestic production processes for laminated metallic armor plates and high strength structural components that can be readily integrated into vehicle structures using existing welding processes. This type of armor and components would allow for significant reduction in weight while maintaining the same level of force protection.
Description
Dual-hardness and tri-hardness laminated and functionally graded armor steel, aluminum, and titanium plate have been researched for decades, e.g. [2-4]. Demonstrated to have high mass efficiencies as compared to traditional monolithic armor plate – in some cases resulting in half the weight of traditional armor materials to defeat equivalent threats – utilization of these advanced, high performance armor systems has been very limited or proven not commercially viable.
Production of these materials has proven difficult to scale cost-effectively, as commercial production practices suffer from plate warpage and waviness, resulting in excessive scrap rates and limited yield. In addition, laminated armor systems have proven difficult to form and join, which restricts their utilization to that of an applique system, rather than their utilization as a fabricated structural component. While high-performing ballistically, ultimately, the cost of the materials and the difficulty in their manufacture and then fabrication into useful structural components has limited their application and commercial viability.
Phase I
This topic is accepting only Phase I proposals for the cost of up to $250,000 for up to a 6-month period of performance.
Demonstrate the feasibility of laminated steel armor:
Phase II
Demonstrate the following:
Phase III
Laminated metallic armor and high strength structural components have a variety of commercial use cases to include Lightweight armor for cars and SUVs for police and VIPs, armor for vaults and safes and wear plate for construction and mining equipment.
Submission Information
All eligible businesses must submit proposals by noon, ET.
To view the full solicitation details, click here.
For more information, and to submit your full proposal package, visit the DSIP Portal.
Applied SBIR Help Desk: usarmy.pentagon.hqda-asa-alt.mbx.army-applied-sbir-program@army.mil
References:
Selectees
Objective
The Army is seeking low-cost, high-yield domestic production processes for laminated metallic armor plates and high strength structural components that can be readily integrated into vehicle structures using existing welding processes. This type of armor and components would allow for significant reduction in weight while maintaining the same level of force protection.
Description
Dual-hardness and tri-hardness laminated and functionally graded armor steel, aluminum, and titanium plate have been researched for decades, e.g. [2-4]. Demonstrated to have high mass efficiencies as compared to traditional monolithic armor plate – in some cases resulting in half the weight of traditional armor materials to defeat equivalent threats – utilization of these advanced, high performance armor systems has been very limited or proven not commercially viable.
Production of these materials has proven difficult to scale cost-effectively, as commercial production practices suffer from plate warpage and waviness, resulting in excessive scrap rates and limited yield. In addition, laminated armor systems have proven difficult to form and join, which restricts their utilization to that of an applique system, rather than their utilization as a fabricated structural component. While high-performing ballistically, ultimately, the cost of the materials and the difficulty in their manufacture and then fabrication into useful structural components has limited their application and commercial viability.
Phase I
This topic is accepting only Phase I proposals for the cost of up to $250,000 for up to a 6-month period of performance.
Demonstrate the feasibility of laminated steel armor:
Phase II
Demonstrate the following:
Phase III
Laminated metallic armor and high strength structural components have a variety of commercial use cases to include Lightweight armor for cars and SUVs for police and VIPs, armor for vaults and safes and wear plate for construction and mining equipment.
Submission Information
All eligible businesses must submit proposals by noon, ET.
To view the full solicitation details, click here.
For more information, and to submit your full proposal package, visit the DSIP Portal.
Applied SBIR Help Desk: usarmy.pentagon.hqda-asa-alt.mbx.army-applied-sbir-program@army.mil
References: